沉浸式高精度数控车床模拟仿真软件智能实训新体验
19429202025-03-21安卓手游7 浏览
一、传统实训高成本低效率,虚拟仿真能破局吗?
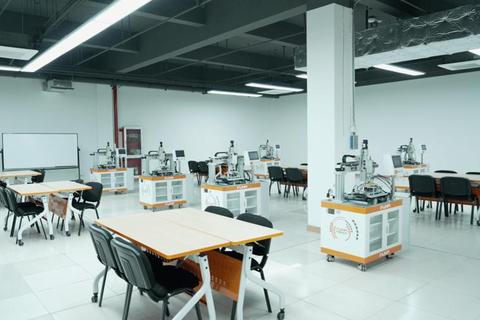
在数控加工教学领域,长期存在“设备贵如黄金,失误代价惊人”的困境。某职业技术学院统计显示,学生初次操作真实数控车床时,因误操作导致的刀具损坏率高达35%,而每台数控机床的维护成本年均超过2万元。更令人揪心的是,由于缺乏真实场景训练,毕业生进入企业后平均需要3-6个月的岗前培训才能独立操作设备。
这种背景下,沉浸式高精度数控车床模拟仿真软件智能实训新体验应运而生。湖南某职业院校引入CK6150数控车床虚拟仿真系统后,学生失误率降低至5%以下,刀具损耗成本缩减80%。这种通过三维建模技术1:1还原真实设备的虚拟环境,让学员在数字空间完成从编程到加工的全流程操作,既规避了物理风险,又保留了真实操作的手感。
二、虚拟仿真如何实现“比真实更真实”?
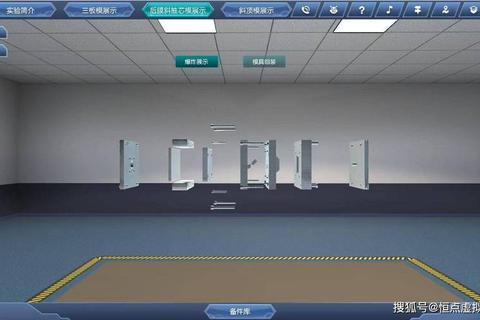
在南京某智能制造实训基地,学员佩戴VR头盔操作虚拟数控车床时,竟能感受到主轴转速变化带来的细微震动——这源于沉浸式高精度数控车床模拟仿真软件智能实训新体验中的物理引擎技术。系统不仅精确模拟了切削力、材料变形等物理特性,还能实时生成金属切削的火花特效和声音反馈。
更突破性的创新体现在智能纠错系统。当学员在沈阳某企业培训中心使用斯沃数控仿真软件时,程序中的刀具路径冲突会被自动标注,系统同步显示三维碰撞动画,并提供优化建议。这种实时反馈机制使学习效率提升3倍,某汽车零部件企业采用该系统后,新员工上岗培训周期从90天压缩至30天。
三、虚拟实训能取代实体设备吗?
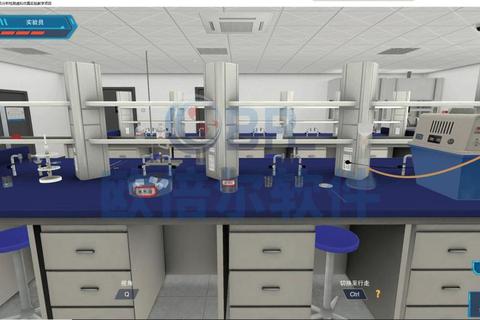
争议的焦点在甘肃某高校得到验证:该校将40%的实训课时改为沉浸式高精度数控车床模拟仿真软件智能实训新体验后,学生在全国数控技能大赛中的获奖率反而提升了25%。其秘密在于虚拟系统独有的“上帝视角”——学员可任意缩放观察刀具与工件的微观接触,这在实体设备上根本无法实现。
但完全替代仍不现实。苏州工业园区某校企合作项目采用“7:3虚实结合”模式,即70%基础操作在宇龙数控仿真系统完成,30%高阶技能在真实设备强化。这种组合使设备利用率从65%提升至92%,同时将耗材成本降低40%。更值得关注的是,系统内置的2000+故障模拟场景,让学员提前掌握90%以上的设备异常处理技能。
从虚拟到现实的跨越指南
对于院校和企业,建议分三步构建智能实训体系:
1. 基础搭建:选择支持B/S架构的仿真软件(如VNUC系统),确保50台终端并发运行时延迟低于0.1秒
2. 进阶融合:部署数字孪生实验室,通过物联网将虚拟操作数据同步至实体机床,实现“虚控实”加工
3. 生态扩展:接入MES系统进行生产模拟,让学生提前适应工业4.0环境下的排产调度
当前市场主流产品中,SolidWorks+VERICUT组合可覆盖85%的数控加工场景,而HyperMill在五轴加工仿真领域精度可达0.001mm。但需注意,优质虚拟实训系统的三大黄金指标是:物理仿真准确度≥98%、指令响应速度≤50ms、支持设备型号库≥200种。
这场数控教育的数字革命已势不可挡——当虚拟与现实的无缝衔接使培训成本降低60%、效率提升300%,沉浸式高精度数控车床模拟仿真软件智能实训新体验正在重新定义制造业人才培养的黄金标准。