超凡智能玻璃优化切割软件赋能高效精准省料新境界
19429202025-03-26单机游戏10 浏览
玻璃切割行业的难题:传统方式是否已走到尽头?
在玻璃加工行业中,材料浪费始终是悬在企业头顶的“达摩克利斯之剑”。据统计,传统人工切割的废料率高达15%-20%,而复杂订单的切割效率甚至不足60%。面对日益激烈的市场竞争,如何打破“高成本、低效率”的困局?当一家企业接到一笔10万平方米的幕墙玻璃订单时,是否只能依靠经验丰富的老师傅“凭感觉”下料?超凡智能玻璃优化切割软件赋能高效精准省料新境界的出现,正在颠覆这一局面。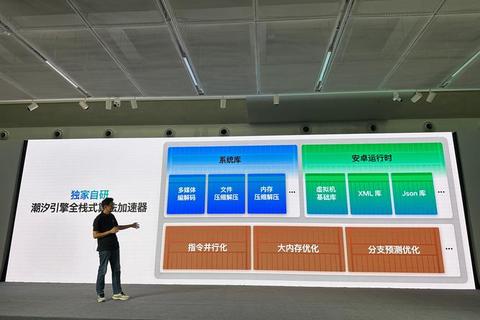
一、如何用算法“榨干”每一寸玻璃?
玻璃切割的核心目标是以最小损耗满足多样化需求。传统人工排料往往依赖经验,但面对上百种尺寸的订单时,难免顾此失彼。例如,山东某玻璃厂曾因一笔包含200多种异形玻璃的订单陷入困境——人工排料耗时3天,废料率仍达18%。引入超凡智能玻璃优化切割软件后,系统通过遗传算法和模拟退火算法,仅用15分钟生成切割方案,废料率骤降至5%,相当于每万平方米节省3吨原片。
该软件的“智能均边”功能尤为亮眼。传统切割常因边角余料(3-8毫米)无法利用而被迫废弃,而软件可将余料自动分摊至相邻玻璃尺寸,甚至通过动态调整磨边量实现“零残料”。例如,某中空玻璃厂商通过此功能,一年节省磨边成本超30万元。
二、精度与效率能否“鱼与熊掌兼得”?
在精度要求严苛的电子玻璃领域,0.1毫米的误差就可能导致整批产品报废。而传统设备往往陷入“精度高则速度慢,速度快则精度低”的怪圈。超凡智能玻璃优化切割软件通过三大创新破局:
1. 设备协同控制:与切割机无缝对接,实时校准参数。某家电玻璃厂使用后,切割速度提升40%,同时将公差控制在±0.5毫米内。
2. 动态路径规划:采用高精度激光定位技术,即使是曲线切割也能实现“一刀成型”。例如,某艺术玻璃厂商加工波浪形装饰玻璃时,废品率从12%降至1%。
3. 异常预警系统:通过物联网传感器监测设备状态,提前预警轴承磨损等隐患。某企业设备故障停机时间因此减少70%。
三、智能管理能否让“余料变黄金”?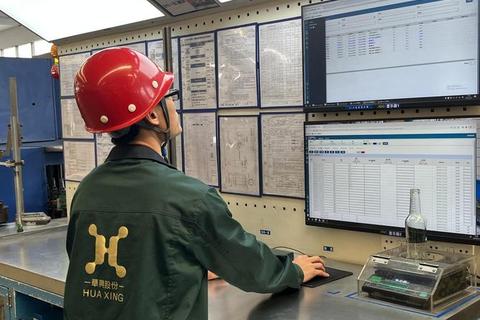
库存积压和余料浪费是玻璃行业的隐形成本。传统模式下,余料管理依赖人工记录,常出现“需要时找不到、找到时用不上”的尴尬。超凡智能玻璃优化切割软件的解决方案是:
智能库存联动:自动扫描仓库原片尺寸,优先调用余料。浙江某企业通过此功能,将5万片历史余料利用率从20%提升至85%。
跨工程优化:支持多项目数据合并分析。例如,某幕墙公司同时处理3个工程的订单时,通过系统整合优化,节省原片采购成本12%。
全流程追溯:从订单导入到成品标签打印,每个环节数据自动归档。某出口企业凭借此功能,将质检效率提升50%,客诉率下降90%。
破局之道:三步实现切割革命
对于希望升级转型的企业,建议遵循“试点-迭代-普及”路径:
1. 优先试用核心模块:选择支持Excel导入、余料管理的版本,用实际订单验证效果(如山东长风软件的试用版)。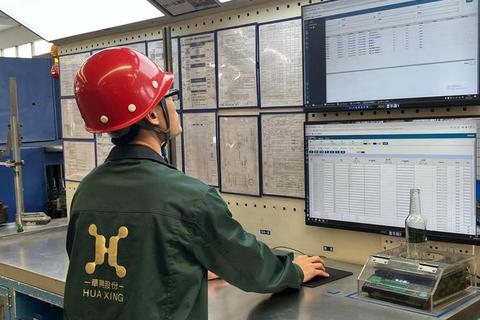
2. 培养复合型人才:结合系统自带的模拟操作和视频教程,提升操作员从“机械执行”到“策略优化”的能力。
3. 建立动态评估体系:定期对比优化率、设备稼动率等关键指标,例如设定“季度废料率下降3%”的阶梯目标。
超凡智能玻璃优化切割软件赋能高效精准省料新境界,不仅是一套工具,更是一种生产思维的进化。当算法开始“思考”如何切割,每一块玻璃的价值都被重新定义——这或许正是传统制造业迈向智能化的关键一跃。